By Girish Linganna
Apr 16: ISRO has made a significant advancement in rocket engine technology by creating a lightweight Carbon-Carbon (C-C) nozzle for rocket engines. This breakthrough, achieved by the Vikram Sarabhai Space Centre (VSSC), has the potential to improve important aspects of rocket engines, such as thrust levels, specific impulse, and thrust-to-weight ratios. As a result, it will increase the payload capacity of launch vehicles.
"Thrust levels" refers to the amount of force or power generated by a rocket engine to propel the rocket forward into space. It's like the engine's strength or pushing ability.
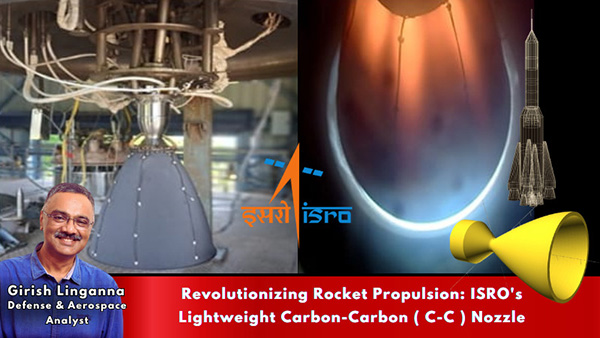
"Specific impulse" is a measure of how efficiently a rocket engine uses propellant to generate thrust. It indicates how much push a rocket gets for each unit of propellant consumed.
"Thrust-to-weight ratio" is a comparison between the amount of thrust generated by a rocket engine and the weight of the entire rocket. It helps determine how effectively the rocket can overcome the force of gravity and accelerate.
The VSSC, known for its groundbreaking space research, has utilized advanced materials like Carbon-Carbon (C-C) Composites to develop a nozzle with outstanding qualities. By employing techniques such as converting green composites into carbon, introducing chemicals through vapor infiltration, and subjecting it to high temperatures, they have produced a lightweight, strong, and rigid nozzle that maintains its mechanical properties even under high temperatures.
Carbon-Carbon (C-C) composites are advanced materials made by combining carbon fibers with a carbon matrix. They are known for their exceptional strength, light weight, and heat resistance, making them ideal for aerospace and high-performance applications.
In this context, "matrix" refers to a material that surrounds and binds together the carbon fibers in a Carbon-Carbon (C-C) composite. It provides structural integrity and helps distribute loads and stresses throughout the material.
"Converting green composites into carbon" means transforming environmentally-friendly composite materials into carbon-based materials. This process involves treating the composites at high temperatures to remove non-carbon elements and enhance their properties for specific applications.
"Introducing chemicals through vapor infiltration" refers to a technique of adding specific chemicals to the carbon composite material by allowing them to penetrate and fill the gaps between carbon fibers using a vapor-based process. This enhances the material's properties and performance.
The C-C nozzle has a unique protective layer made of Silicon Carbide, which helps it withstand harsh conditions and high temperatures in environments with oxygen. This special coating not only reduces stress caused by heat but also improves the nozzle's ability to resist corrosion. As a result, the C-C nozzle can operate at higher temperatures in challenging surroundings.
Silicon carbide is a type of material that is made up of silicon and carbon atoms. It is known for its exceptional hardness, high thermal conductivity, and resistance to extreme temperatures and chemical corrosion.
This development has a significant potential impact, especially for the Indian Space Research Organisation (ISRO)'s primary launcher, the Polar Satellite Launch Vehicle (PSLV). The fourth stage of the PSLV, known as PS4, currently uses twin engines with nozzles made of Columbium alloy.
The PS4 stage is the uppermost part of the PSLV and consists of two liquid engines that can be stored at room temperature on Earth.
By replacing the metallic divergent (expnding property) nozzles of the PS4 stage with C-C counterparts, a significant weight reduction of around 67% can be achieved. This substitution is expected to increase the PSLV's payload capacity by 15 kg, which is a notable improvement for space missions.
The testing of the C-C nozzle's expanding section was a significant achievement for ISRO. On March 19, 2024, a 60-second hot test was conducted at the High-Altitude Test (HAT) facility in ISRO Propulsion Complex (IPRC), Mahendragiri. This test confirmed that the system performed well and the hardware remained intact. Additional tests, including a 200-second hot test on April 2, 2024, further confirmed the nozzle's capabilities. The tests successfully reached temperatures of 1216K,(943.85 degree centigrade) matched the predicted values.
The testing process involved collaboration between two organizations: the Liquid Propulsion Systems Centre (LPSC) at Valiamala, responsible for designing and setting up the test, and IPRC, Mahendragiri, which conducted the actual tests and handled the instrumentation at their HAT facility.
(The author Girish Linganna of this article is a Defence, Aerospace & Political Analyst based in Bengaluru. He is also Director of ADD Engineering Components, India, Pvt. Ltd, a subsidiary of ADD Engineering GmbH, Germany. You can reach out to him at: girishlinganna@gmail.com)